Your food scraps will be used to make nutrient-rich compost and clean energy!
All food scraps collected in Boston will be recycled instead of wasted. This includes composting via turned windrows in Brockton, Massachusetts, or recycling at the CORe facility in the Charlestown Maritime District of Boston. It is our goal is to expand composting operations to eventually process all of Boston's food waste. In order to meet the capacity needs of a municipal-scale program for Boston, we will rely on both composting and anaerobic digestion based on current infrastructure. If you have a permitted composting facility and are able to accept food waste, contact us!
There are numerous benefits to preventing the landfilling and incineration of food scraps and organic materials. These make up roughly 40% of our landfills, where they emit high levels of greenhouse gases. It is inefficient and costly to incinerate organic materials in our waste. Composting is a way for nutrients to be returned to the soil to the benefit of our community and our environment. By applying compost as a natural soil amendment, we improve biodiversity rather than destroy it. This improves the long term health of the soil which has environmental benefits. Healthy soil stores carbon, improving air quality. Soil health and structure prevent erosion, and store water. This also keeps our waterways clean by preventing run off. The process of anaerobic digestion harnesses the energy potential of organic waste by transforming your food scraps into biogas. This can be used to create green energy. A byproduct of this process called digestate can be used as fertilizer. While requiring high-tech equipment, anaerobic digestion is a space-efficient process. This makes it ideal for use in urban centers like Boston.
COMPOSTING
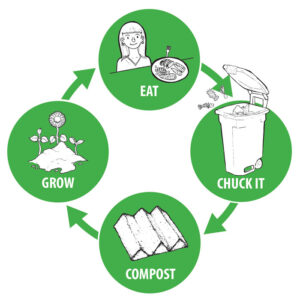
The process of composting involves creating the optimal conditions to facilitate an efficient and effective decomposition of organic materials. The result is a nutrient-dense, locally sourced, high quality soil amendment. The method used at the composting facility in Brockton is windrow composting.
Food scraps delivered to the site are combined with leaf and yard waste, and forestry byproducts such as sawdust, in long piles called "windrows." These active compost piles rapidly reach temperatures over 131 degrees Fahrenheit because of the energy produced by heat-loving bacteria. These high temperatures and microorganisms are able to break down complex organic materials quickly, eliminating the risk of pathogens and disease. This enables us to collect a wider range of items than should be included in a home composting system, such as meat, dairy, and bones.
The piles are turned with loaders and excavators as needed to ensure proper aeration and moisture levels. As our compost matures, we carefully monitor the soil to ensure ideal levels of nitrogen, phosphorus, and other nutrients, as well as optimal pH and stability. Always dedicated to quality, we develop our soil for over 12 months into the finished product: a nourishing, long-lasting compost. Residents that receive food waste collection will be able to log into their online account to purchase bagged compost for delivery.
Interested in learning a lot more about composting? Check out the annual Boston Compost Certificate Program here!
ANAEROBIC DIGESTION
(Images courtesy of WM)
In anaerobic digestion, bacteria break down organic matter (like animal manure and food waste) in the absence of oxygen. Food scraps processed by anaerobic digestion are blended into a slurry at the WM CORe facility in Charlestown, MA. After being pretreated to remove contamination, it is transported to North Andover’s GLSD anaerobic digestion facility where it is fed into a digester. Inside the digester, the materials are in optimal conditions for converting the organic waste into biogas using natural microorganisms. The process is similar to composting, but in the absence of oxygen, the food scraps are converted into biogas instead of soil. This biogas is captured and used to make green energy. The vast majority of the food waste (90% of the material) is converted to biogas. A very small portion of material, roughly 10%, is not converted and ends up in the dried fertilizer product.